Executive Summary
Key companies driving innovations in the field include 3D Systems, EOS GmbH, and GE Additive. All of these are major companies pushing metal printing technology ahead of schedule as the market expands with aerospace, automotive, healthcare, and consumer goods companies clamoring for a greater supply. Using 3D metal printing for high-precision speed and customized components is providing lightweight complex pieces needed for a wide variety of applications in specific industries.
Attributes |
Details |
Projected Size, 2035 |
USD 12 billion |
Value-based CAGR (2025 to 2035) |
11.2% |
Continuous improvement for vendors would focus more on the metal powders, including developments in titanium, aluminum, and stainless steel. These advancements further enhance the performance of the material, which works well in high-stress critical applications, but most importantly in aerospace and healthcare fields. Companies are also spending money on R&D to refine printing techniques and produce the next generation of printers that deliver higher speed, accuracy, and scalability.
Sustainability is an important priority; additive manufacturing minimizes material waste significantly compared to subtractive methods. It also aligns with the industry-wide sustainability goals and regulatory pressures. Further, strategic collaborations and partnerships with OEMs and industrial clients help manufacturers provide end-to-end solutions from design to production.
With a forecasted CAGR of 11.2%, and the market expected to touch more than USD 12 billion in 2035, vendors and manufacturers are exploring this growth further by innovating their portfolios, expanding their footprints globally and meeting the continuously evolving needs of customers.
Explore FMI!
Book a free demo
Adoption Drivers
- Enhanced Design Freedom: Businesses capitalize on the geometric flexibility offered by 3D printing to produce intricate designs.
- Rapid Prototyping: Companies utilize 3D metal printing to accelerate product development cycles and reduce time to market.
- Cost Efficiency: The technology reduces tooling costs, making it particularly advantageous for low-volume production runs.
Vendor Performance
Global Market Share & Industry Share (%), 2025E
Category |
Industry Share (%) |
Top 3 (3D Systems, EOS GmbH, GE Additive) |
45% |
Rest of Top 5 (Renishaw, SLM Solutions) |
10% |
Next5 of Top 10 Players |
5% |
Type of Player & Industry Share (%), 2025E
Type of Player |
Industry Share (%) |
Top 10 |
60% |
Next 20 |
25% |
Remaining Players |
15% |
Market Concentration, 2025E
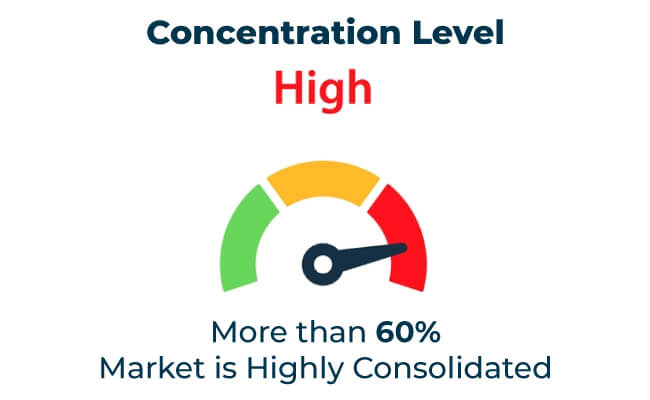
Year-over-Year Leaders
- 3D Systems: Maintains a leadership position with advanced metal printing systems and software.
- EOS GmbH: Excels in providing industrial-grade metal printing solutions for aerospace and medical applications.
- GE Additive: Pioneers innovations in additive manufacturing technologies and material development.
Technology Trends in the 3D Printing Metal Market
- Multi-Laser Printing: Companies adopt multi-laser systems to improve print speed and reduce production costs.
- Hybrid Manufacturing: Firms integrate 3D metal printing with traditional manufacturing methods to enhance production efficiency.
- Metal Binder Jetting: Innovations in binder jetting technology enable cost-effective and large-scale production of metal parts.
- Recyclable Powders: Manufacturers develop recyclable metal powders to minimize waste and improve sustainability.
Sustainability Trends
- Energy Efficiency: Companies prioritize energy-saving practices during the metal printing process to reduce environmental impact.
- Closed-Loop Systems: Businesses adopt closed-loop powder recycling systems to maximize material utilization.
- Lightweight Components: Industries produce lightweight metal parts to improve fuel efficiency in automotive and aerospace sectors.
Consumer Trends
- Demand for Custom Products: Consumers increasingly seek personalized goods, driving demand for 3D metal printing in consumer products.
- Preference for Eco-Friendly Solutions: Buyers favor products made with sustainable manufacturing technologies.
- Interest in High-Quality Products: Consumers value the precision and durability offered by 3D metal-printed components.
Regulatory Insights
- North America: Supportive policies and government funding boost the adoption of additive manufacturing in critical industries.
- Europe: Stringent quality standards in aerospace and healthcare drive innovation in 3D metal printing.
- Asia-Pacific: Rapid industrialization and investments in advanced manufacturing technologies foster market growth.
- Emerging Markets: Countries in Africa and Latin America increasingly adopt 3D metal printing to enhance industrial capabilities.
Export Opportunities
Emerging markets in Southeast Asia, Africa, and South America provide significant export opportunities for 3D metal printing solutions. The growing demand for advanced manufacturing technologies and custom components supports market expansion.
Challenges and Opportunities
Challenges
- High Initial Costs: The cost of 3D metal printers and associated materials limits adoption for small and medium enterprises.
- Material Limitations: Limited availability of certified metal powders restricts applications in certain industries.
- Technical Expertise: A shortage of skilled professionals hampers the efficient adoption of 3D metal printing technologies.
Opportunities
- Emerging Applications: Industries explore new applications for 3D metal printing, including energy storage and medical implants.
- Collaborative Research: Partnerships between manufacturers, universities, and research institutions accelerate technological advancements.
- Government Support: Incentives and funding initiatives promote the adoption of 3D metal printing in developing economies.
Market Context
Regional Analysis
Region |
North America |
Market Share (%) |
40% |
Key Drivers |
Advanced manufacturing infrastructure and strong aerospace sector |
Region |
Europe |
Market Share (%) |
30% |
Key Drivers |
High demand for precision components in automotive and healthcare |
Region |
Asia-Pacific |
Market Share (%) |
20% |
Key Drivers |
Growing investments in industrial automation and additive manufacturing |
Region |
Other Regions |
Market Share (%) |
10% |
Key Drivers |
Increasing adoption in emerging markets |
End-Use Industry Segments
- Aerospace: Dominates the market with applications in lightweight and high-strength components.
- Automotive: Utilizes 3D metal printing for prototyping and producing performance-enhancing parts.
- Healthcare: Employs additive manufacturing for custom medical implants and surgical instruments.
Recommendations for Technology Suppliers
- Invest in Training Programs: Companies should collaborate with educational institutions to develop skilled professionals for 3D metal printing.
- Focus on Material Development: Expanding the range of certified metal powders will unlock new applications and markets.
- Enhance Scalability: Manufacturers should prioritize the development of cost-effective and scalable solutions for mass production.
Future Roadmap
The 3D printing metal market will continue to grow as industries prioritize efficiency, precision, and sustainability. Companies that address challenges such as material limitations and cost barriers while investing in innovation will lead the market. Emerging applications in energy, healthcare, and aerospace will further drive adoption and market expansion.
Market KPIs
- Regional Revenue Growth: Businesses should monitor market performance in Asia-Pacific and emerging economies.
- Application-Specific Metrics: Companies should evaluate the adoption of 3D metal printing in aerospace, automotive, and healthcare sectors.
Who Shaped the Year
- 3D Systems: Leads the market with advanced and sustainable metal printing technologies.
- EOS GmbH: Expands its portfolio with industrial-grade metal printing solutions.
- GE Additive: Focuses on innovative materials and scalable manufacturing technologies.
Key Players
Tier |
Key Companies |
Tier 1 |
3D Systems, EOS GmbH, GE Additive |
Tier 2 |
Renishaw, SLM Solutions |
Tier 3 |
Desktop Metal, Materialise |
Key Vendor Initiatives
- 3D Systems: Invests in advanced software and hardware solutions to enhance productivity.
- EOS GmbH: Develops high-performance materials for critical applications.
- GE Additive: Innovates with hybrid manufacturing systems that integrate additive and subtractive methods.
Conclusion
The 3D printing metal market transforms manufacturing by enabling efficient, precise, and sustainable production. Companies focusing on material innovations, collaborative research, and emerging applications will shape the future of this dynamic sector. Addressing challenges such as cost and technical expertise will unlock significant growth potential, ensuring 3D metal printing remains a cornerstone of industrial evolution.
Appendix
Key Definitions
- 3D Printing Metal: Additive manufacturing technology that uses metal powders to create intricate and high-strength components.
- Binder Jetting: A 3D printing process that uses a binding agent to join metal powder particles.
- Closed-Loop Recycling: A system where metal powders are reused multiple times in the manufacturing process.
Research Methodology
This report synthesizes data from primary interviews, secondary research, and market modeling validated by industry experts.
Frequently Asked Questions
What will be the growth of 3D printed metal market?
The global 3D printed metal market is projected to witness a CAGR of 11.2% between 2025 and 2035
What will be the worth of global 3D printed metal market by 2035?
The global 3D printed metal market is expected to reach USD 12 Billion by 2035
What is the share of top 10 players in the 3D printed metal market?
The share of top 10 players is 60% in the global 3D printed metal market.
Who are the key manufacturers of 3D printed metal?
3D Systems, EOS GmbH, GE Additive are few of the leading manufacturers of 3D printed metal